Episode 8: Thoughts of the Yamanashi factory inherited to the new factory
2018-01-18
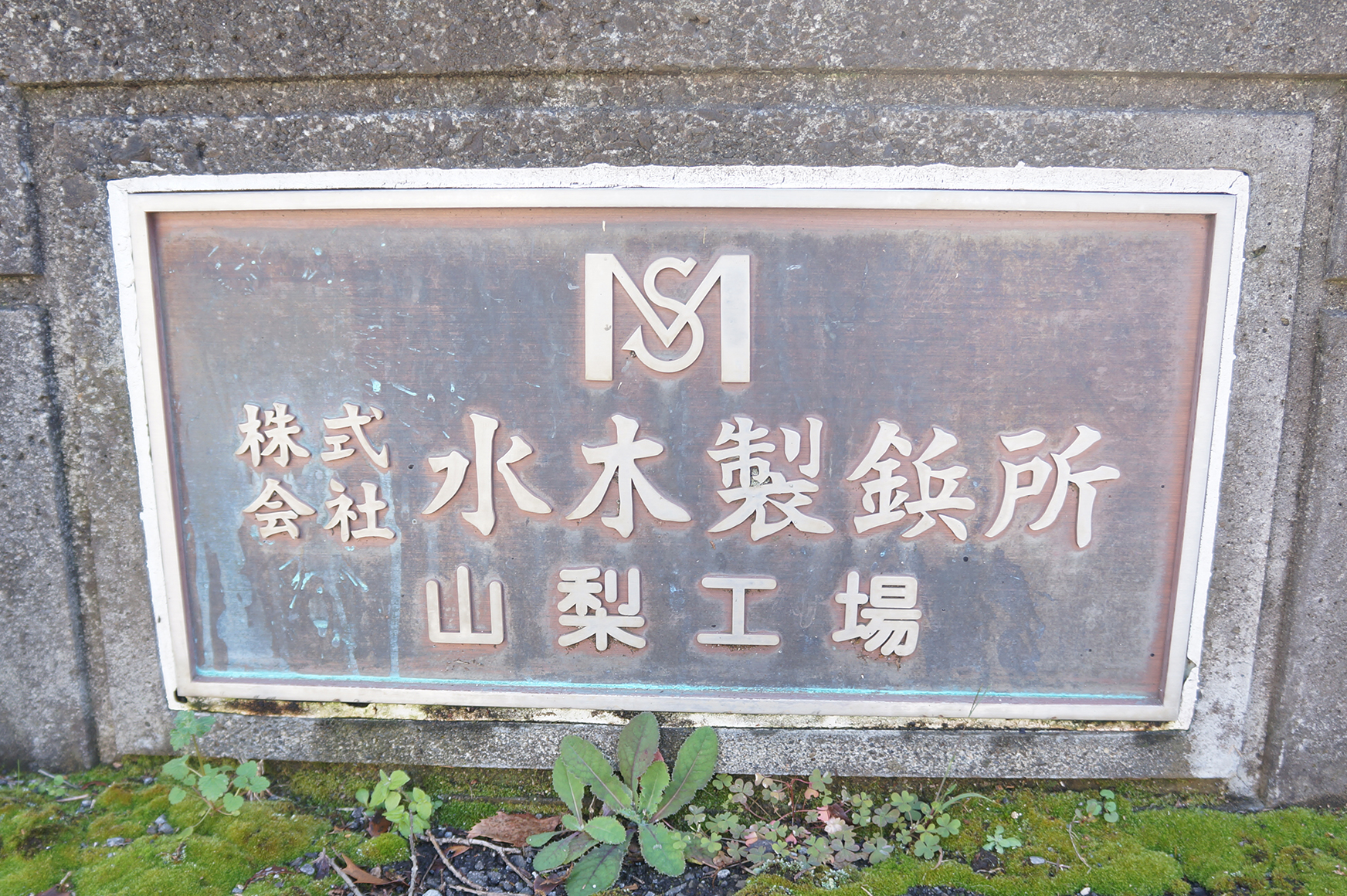
Starting December 1, 2017, the new factory is in full swing, and the days in a brand new work environment has been started.
As the new factory was established, the head office factory and the Yamanashi factory were integrated, so seven staff members belonging to the Yamanashi factory joined the head office factory.
The Yamanashi factory has been mainly producing parts with an outer diameter of 4 mm or less. Small parts are difficult to maintain their accuracy, so you need high expertise and skills. As a result, the Yamanashi members advanced MIZUKI quality, and Yamanashi factory was a place for raising and generating excellent engineers. This time, we talked to three people who belonged to the Yamanashi Factory. We could gain a confidence that the technology and thoughts cultivated at the Yamanashi factory will be merged with the head office factory by the interviews.
Yamanashi Factory which started with only three machines
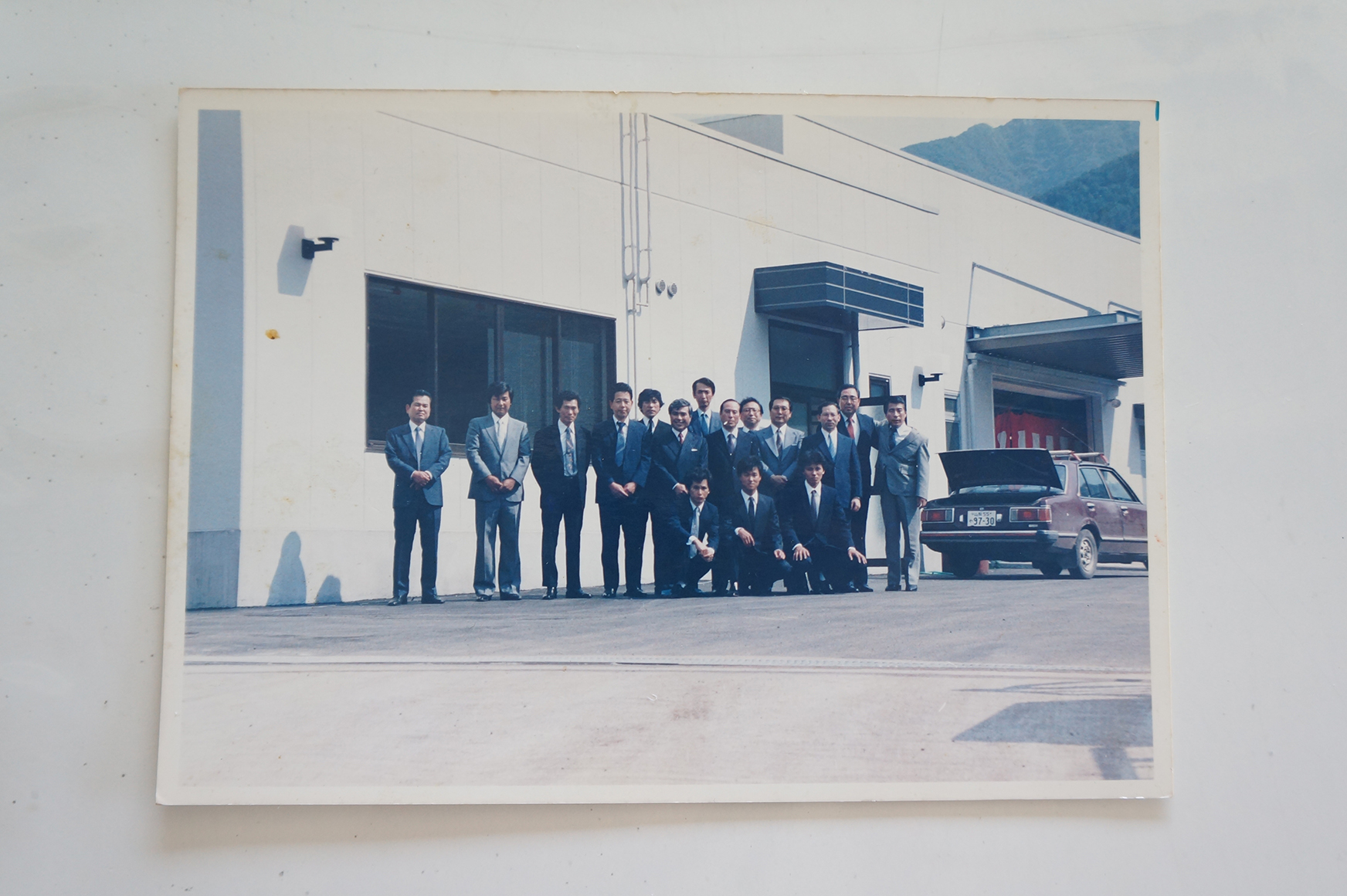
In 1986, the head office factory was located in Machida city, Tokyo. At that time, the city was basically a residential neighborhood, so that it was difficult to operate 24 hours a day while producing manufacturing noises. The Japanese economy has reached its growth stage, and our company was also under pressure to expand the factory to raise the production capacities. Mr. Rikuro Mizuki, previous president, had decided to establish a new factory in Tsuru city, Yamanashi Prefecture, which was not too far from the head office, and had an environment suitable for the factory.
In order to ensure efficient and high productivity, the Yamanashi factory produced the precision screws with φ4 or less, especially φ1.6 or less, while the head office factory quarters in charge of larger screws. The Yamanashi factory was a severe workplace where technologies are required in units of 1/1000 millimeters, and they say that it was also a place to hone the skill of each and every one. Mr. Omata, who worked at the Yamanashi Factory for 17 years and now is one of the chiefs of the manufacturing engineering department, says:
“In the Yamanashi factory, there are only eight people in total. It was a charming atmosphere, and enjoy barbecue with their family members because it was a small group. On the other hand, their products requires very precise technology, and there was a culture climate that enhances technical skills by working hard together, and crossing the walls of seniors and juniors during work. Unity was our pride. ”
A letter of appreciation, delivered to the Yamanashi factory
The Yamanashi Factory, which has been functioning as a manufacturing base for components requiring higher precision, had no sales department. It was extremely rare to interact directly with customers. Therefore, few people outside the company to know the existence of the Yamanashi Factory. However, he says that a letter has delivered to the Yamanashi factory.
When we asked about the most impressive memory about the Yamanashi factory, Mr. Omata talked about the letter.
“We have received a letter from a business partner. There were the words of appreciation for the product we dealt with. Because it was not delivered directly from the Yamanashi factory, I think that the staff of the sales department probably told the customer about the Yamanashi factory. We do not talk to or meet with our customers. So, we are very happy to have a voice of appreciation directly from our customers, and it is still engraved in our memory. It pleased us to work hard, and gave us the power to move forward, and to try hard to please our customers more.”
Currently, Mr. Omata commutes to the new factory by car from his home in Yamanashi.
He said “it was like changing jobs” about working at the new factory. He also says he wishes to raise the level of technical skills that he has been engaged in manufacturing for 17 years with pride. p>
“We are grateful that the parts we make are thankfully used for very expensive items. If I were the customer, I regretted there was poor quality parts in the items I purchased. I do not let the customers regretted. Such feelings have been a driving force for honing skills for the last 17 years. Of course, I continue to hone my skills, and I also train young people who carry on MIZUKI. “ P>
I was glad and trembled at the site of manufacturing
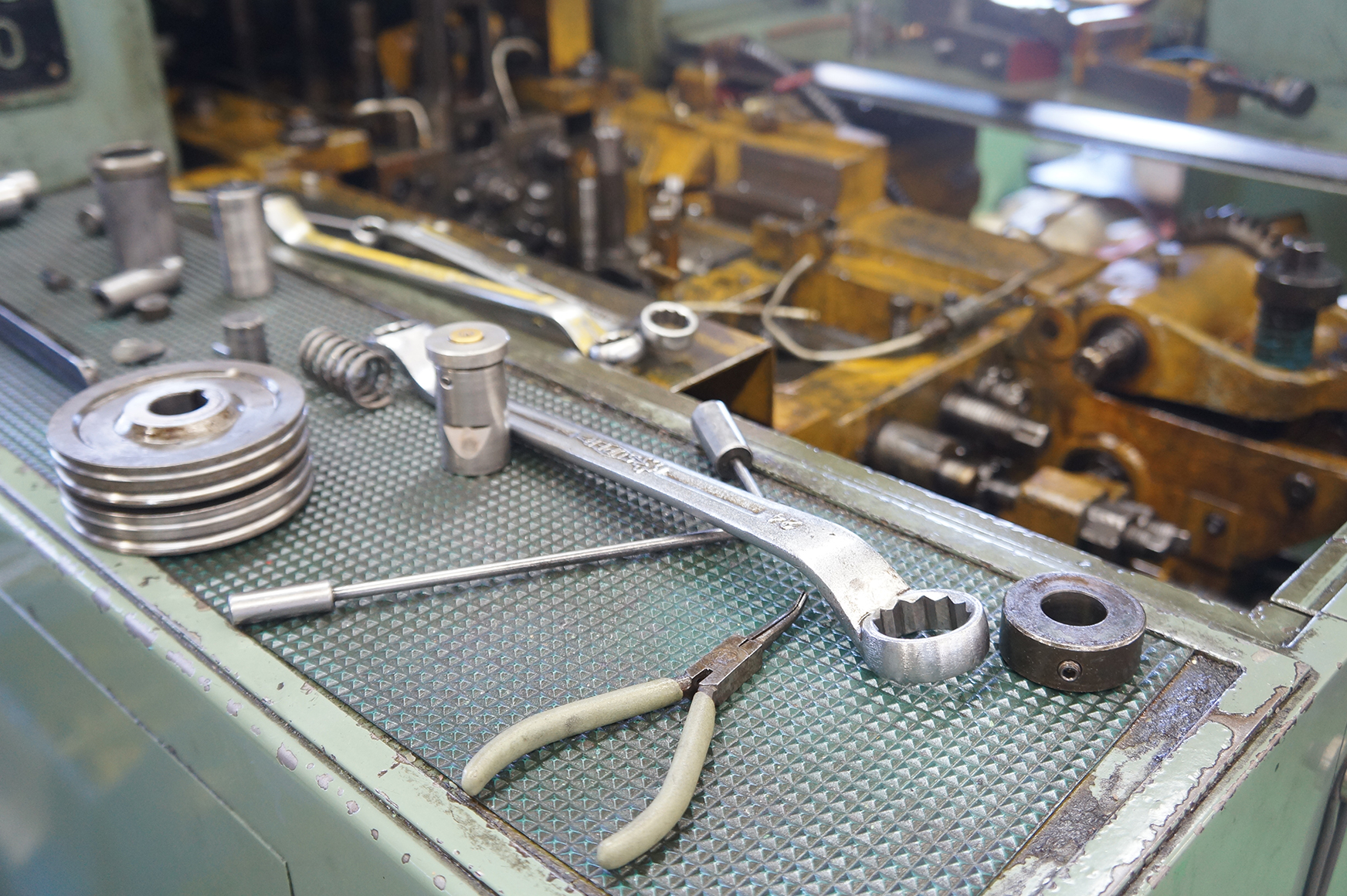
We also interviewed Mr. Yamanashi, who served as a leader engineer at the Yamanashi factory. Mr. Yamanashi has been at the Yamanashi factory for three years after he transferred from the head office to acquire skills. In the head office factory, he have worked for screws with 0.8 millimeters to 4 millimeters, which he had never dealt with at the head office.
He had no trouble to check the screws in his naked eyes when he was at the head office factory. However, it is too small to check the screws in the Yamanashi factory. Engineers in the Yamanashi factory check such screws by touching and utilizing many years of experience and intuition.
“I wonder if I can do it …”
He have been supported by engineers in the Yamanashi factory, especially Mr. Sato who was in service for more than 20 years and in charge of training. p>
“The seniors taught me how to proceed with my work. They did not mad at me when I made mistakes. Instead, they taught me to think what I should do next.
While after I joined at the Yamanashi factory, they told me that it is OK to fail or take a long time. Anyway, just do it from the beginning to the end alone. It took me surprisingly long time, but I managed to complete all processes alone. The seniors who kept watching carefully started to please me by clapping my shoulder. At that moment, I felt that Manufacturing was really interesting from the bottom of my heart. Thereafter, since I had such experience, I have a new perspective of how efficiently produce quality products. “
Be an engineer with good hands and ideas
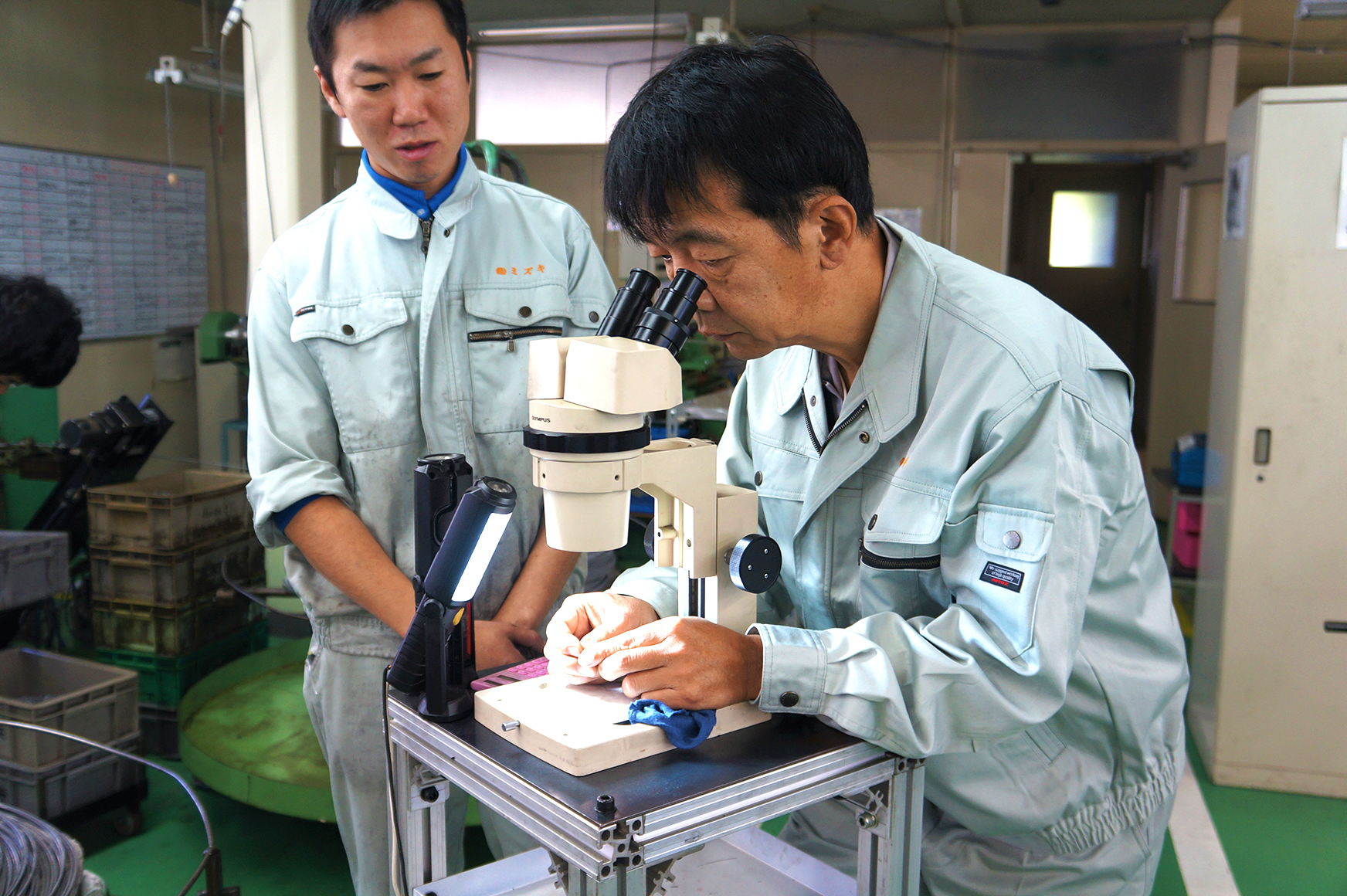
Mr. Sato who was in charge of training Mr. Yamanashi was a valuable existence, since he had worked at the Yamanashi factory for the longest and knew the company’s difficult times. Accuracy required by customers is increasing year by year. He was the one who recognizes the importance of technology inheritance to grow further in the future.
Mr. Sato said as follows after reviewing his experiences to inheritances of Mizuki’s manufacturing.
“There are various people. Some are quick learners, and some can not obtain the skills right away. So, I have been teaching from a viewpoint,” How could I teach him if he was a child? ” I was often asked, “How can I be Mr. Sato?” Every time I answered, “I made mistakes as you are doing over and over again and again. It is a custom to think about how to make it succeed the next time because I experienced more failures than other. ”
Mr. Sato decided to leave MIZUKI at the closing of the Yamanashi factory. Everybody including Mr. Mizuki asked him to change his mind. However, he said “I taught my juniors what I can do as much as possible. I am grateful if they can do what I taught a few years later.”
“There were so many things in 20 years of work, but MIZUKI has good bosses, good colleagues anytime. In the last few years, I was in charged of training young people. I devoted myself for manufacturing and handed over what I got here to the next generation. In my frank opinion, I went through the inheritances. I am willing to give each of my members of the Yamanashi factory a letter of appreciation and diploma. ”
I asked a member who move from the Yamanashi Factory to the head office. They answer “MIZUKI does not grow in a friendly group. We want you to be ” friends” in a true meaning that you can tell anything bad and good.”
A baton from the Yamanashi factory
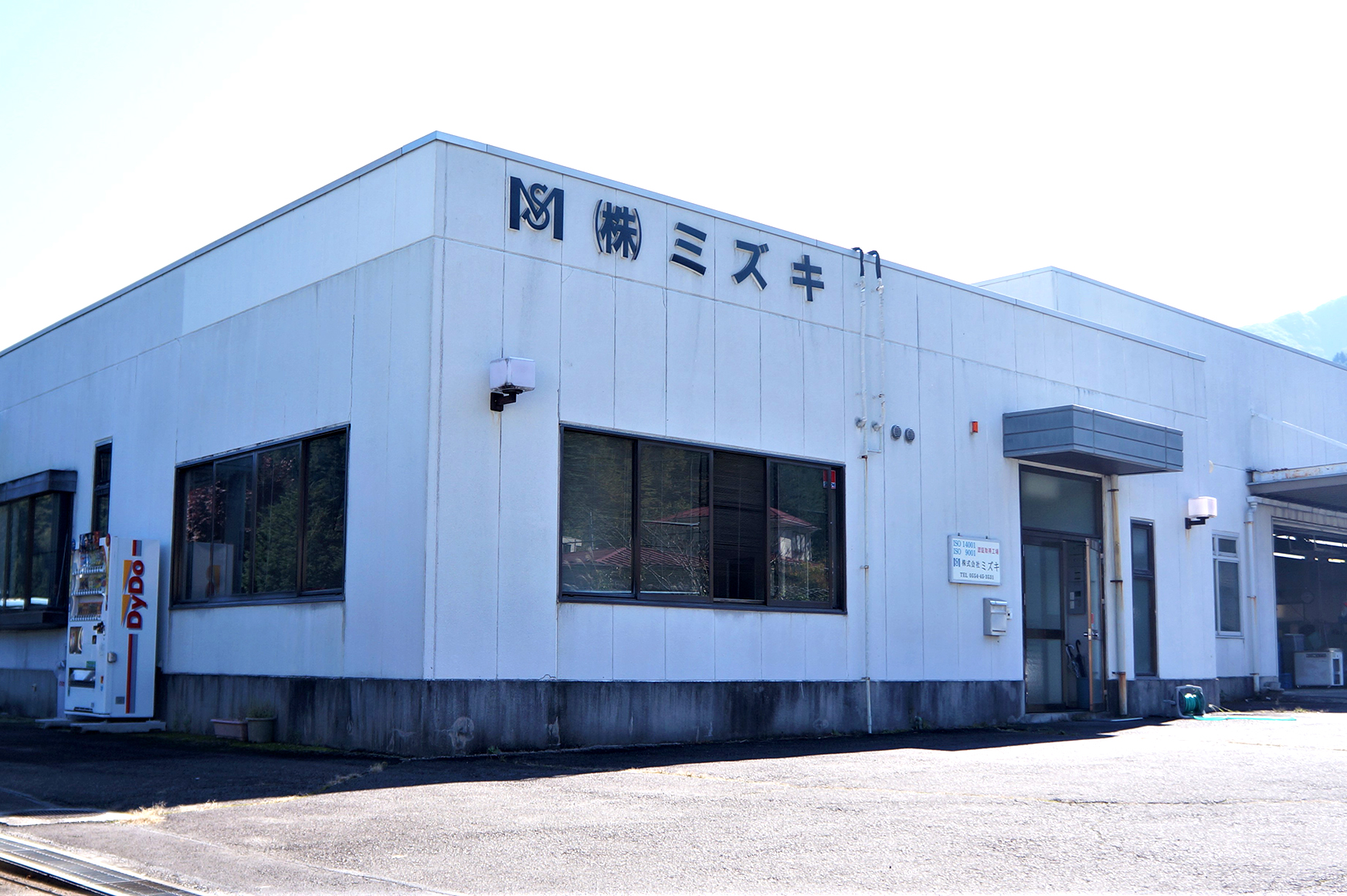
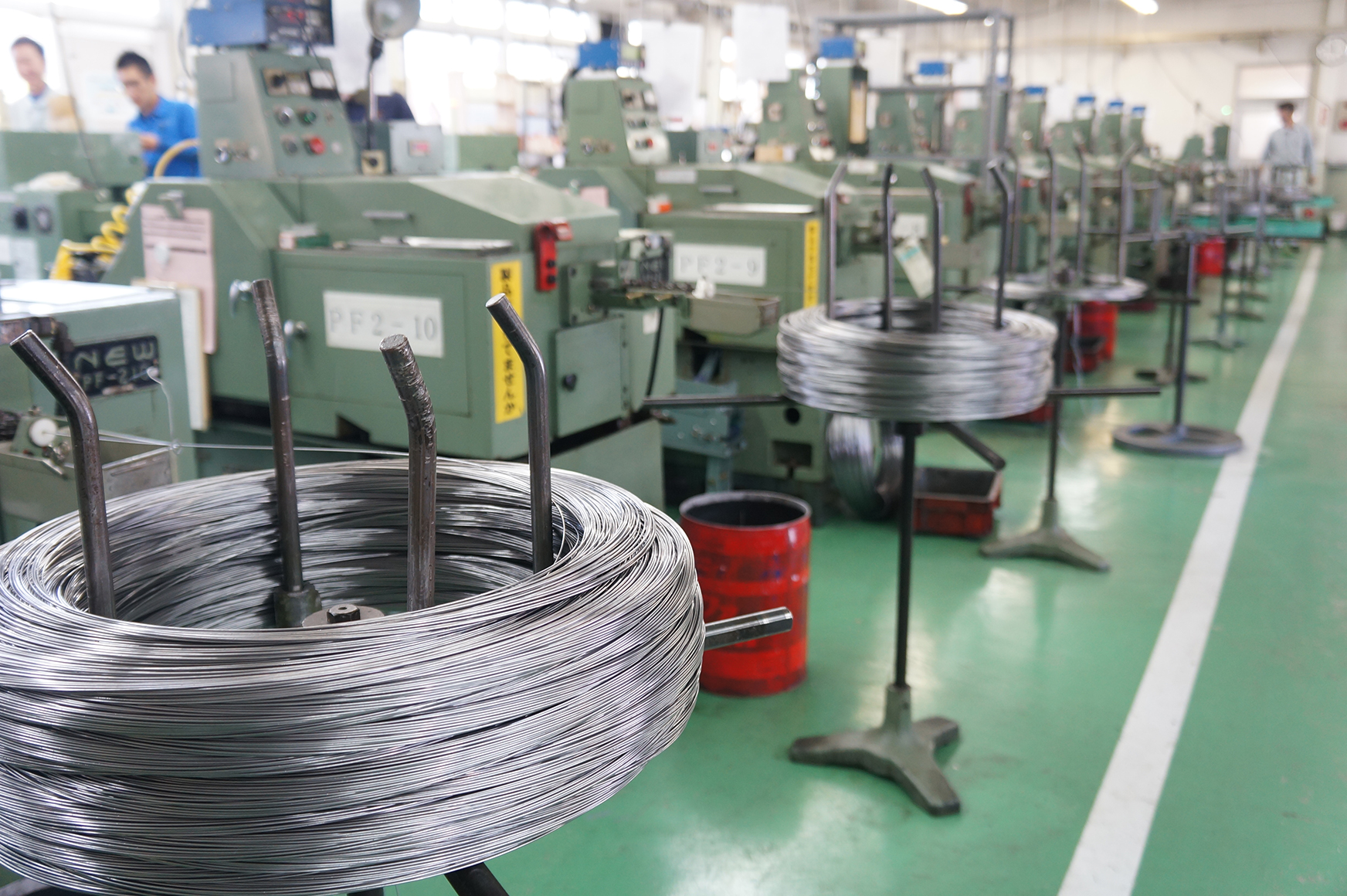
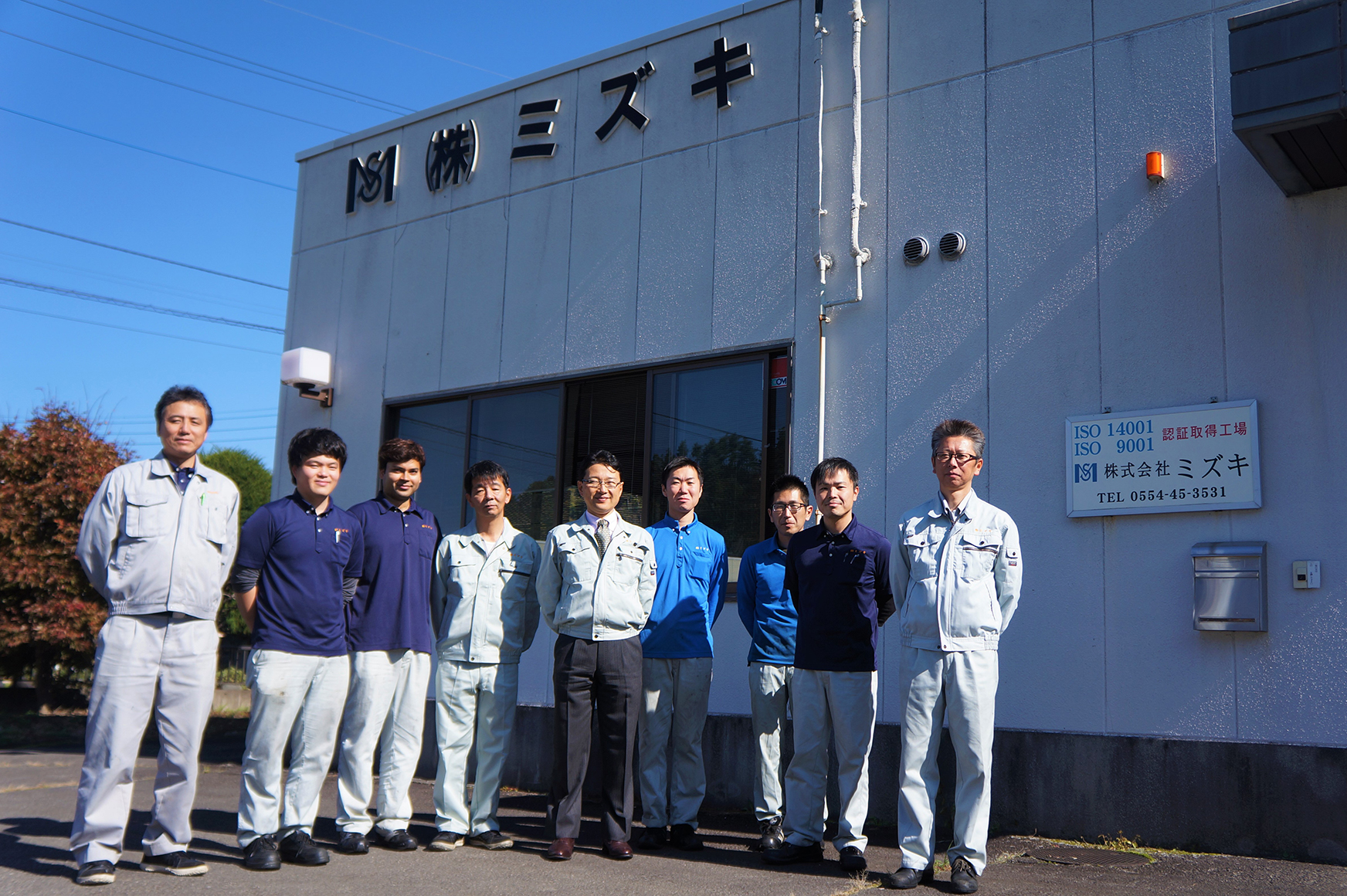
In the background of the integration of the Yamanashi factory, MIZUKI determined to provide overwhelmingly fast and high-quality delivery by concentrating engineers and production bases.
Mr. Mizuki, president, told the members who moved from the Yamanashi factory as follows.
“Since the Yamanashi factory has mainly dealt with the manufacture of screws with an outer diameter of 4 mm or less, you have expertise for precise manufacturing. You have thoughts to take in new technologies curiously. I would like to show the goodness of the small group with unique awareness at the head office as well “
For the Yamanashi members, working at the new factory is busier than before and increases their works. Mr. Mizuki said “I want to prepare an environment where they can concentrate on their works to show their strength built at the Yamanashi factory. It is my role.”
New Mizuki started by mixing the head office and the Yamanashi factory to become a team to impress our customers.
It is time to inherit the skills and thoughts of the seniors who have built up MIZUKI and to create MIZUKI for our future.